What is DTF Heat Transfer Printing? How to Choose a Heat Transfer Printer?
June 16, 2025
DTF white ink heat transfer printers are a type of digital garment printing equipment, widely recognized for applications such as T-shirt heat transfers. Currently, the garment printing market and demand continue to grow strongly, with DTF printing being one of the primary production methods in this market, accomplished using DTF printers. Selecting a truly suitable DTF printer is a direct factor in the success of a printing business and the most critical part of investing in or operating a garment printing store.
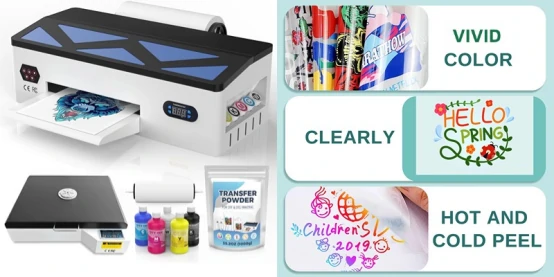
It is widely used in the printing and production of various products. Below are its main application areas and suitable products:
1. Garment Printing
T-shirts, hoodies, sweatshirts, jeans, sportswear, socks, gloves, dresses, bikinis, clothing labels.
2. Accessory Customization
Hats (baseball caps, beanies, etc.), backpacks, handbags, waist bags, aprons, safety vests.
3. Home Decor
Pillows, cushions, canvas bags, curtains, rugs.
Advantages
– Compatibility with various materials: Suitable for cotton, polyester, nylon, silk, and other fabrics.
– Vibrant colors: Achieves bright colors even on dark fabrics.
– Eco-friendly: Inks and processes comply with environmental standards.
– Easy operation: No complex plate-making required, ideal for small batches and personalized production.
To help you choose the right DTF equipment for your printing business, the following will be covered:
– What is a DTF printer?
– Why choose a DTF printer? What are its advantages?
– Key factors in selecting a DTF printer:
– Understanding printing needs
– Important components of a DTF printer
– DTF printing consumables
– Print quality
What is a DTF White Ink Heat Transfer Printer?
The term “DTF” originates from “Direct to Film Printer,” which involves printing designs directly onto PET film, evenly sprinkling hot-melt powder over the pattern, melting it at high temperatures, and drying it. The PET film is then cut, and the design is heat-pressed onto various garments using a heat press machine to complete the garment printing process.
Why focus on this garment printing method? Since 2021, this method has continuously captured market share in garment printing, becoming one of the mainstream techniques. According to Google Trends, searches for “DTF Printer” have been steadily rising since 2021.
A significant reason for the popularity of DTF printers lies in their unique advantages: convenient printing, short preparation cycles, fast printing speeds, high production efficiency, and reliable output quality. Whether meeting bulk printing demands during peak seasons or urgent custom orders during off-seasons, DTF printers handle them effortlessly.
Advantages of DTF Printers:
Compared to DTG (Direct to Garment) printing, DTF printing eliminates the need for pre-treatment sprays, simplifying the process. Unlike screen printing, which requires plate-making, film creation, and other complex steps, DTF printing only requires designing the artwork in graphic software and following technical guidance to complete the steps of printing, powder application, drying, and heat pressing.
DTF prints are wash-resistant and scratch-resistant, with a colorfastness rating of 4-5. For example, a summer T-shirt washed three times a week can last up to two years.
Compared to DTG and sublimation printing, DTF printing breaks the limitations of these methods and offers broader applications. It can be used on cotton, polyester, wool, nylon, spandex, linen, denim, silk, and other fabrics. Essentially, the DTF printer is the “universal printer” of the garment industry.
Before DTF printing emerged, screen printing was one of the giants in garment printing. The advent of DTF printing provided manufacturers with a versatile alternative.
Screen printing is renowned for bulk production, offering reliable speeds during peak seasons. However, its preparatory stages are time-consuming and generate significant wastewater and pollution. From an environmental perspective, DTF printing is superior: it produces no waste gas or water during printing, as machines are equipped with smoke purifiers to process exhaust internally. Operators need only prevent hot-melt powder spillage during printing.
How to Choose the Right DTF Printer?
DTF printers vary in configuration and price. More features and higher configurations lead to higher costs. But does that mean you should always opt for the highest configuration with all features? The answer is: suitability matters most. Beyond traditional manufacturers, emerging DTF printer manufacturers often offer more innovative designs, better leveraging DTF printing advantages and aligning with local markets.
Specifically, selecting the right DTF printer for your garment printing business requires careful consideration of the following factors:
1. Choose Based on Market and Business Needs
DTF printers come in various types:
– High-precision, high-quality A3-sized DTF printers for small-volume but ultra-high-quality T-shirt printing.
– Large-format, high-performance DTF printers for bulk production, oversized prints, or special finishes.
– Models with 4 or 5 printheads for stable, high-speed output, meeting garment factory demands.
As a business owner, you should understand your local printing market, demand, and characteristics. Ask yourself:
– How large is the market demand?
– How many orders do you receive?
– What are the printing volumes?
– Are demands consistent between regular and peak seasons?
– Are there special printing needs (e.g., oversized prints, full-black designs, extra wash- or scratch-resistance)?
– Are there urgent or unexpected orders?
With these answers, clarify your market and business needs, then match them with the printer types mentioned above to narrow down your options.
2. Key Components of a DTF Printer
Understanding DTF printer configurations and critical components is essential for making the right choice. Otherwise, you may feel lost when encountering technical parameters or names. More importantly, you might not grasp why seemingly similar printers vary significantly in price—some due to overpriced “brands” that aren’t necessarily worth it, while others offer high performance hidden behind specs but are overlooked for being “new brands.” As a savvy investor, try to avoid these pitfalls.
Below are some key components:
– Printhead: The printhead is one of the most critical parts of a DTF printer, determining printing performance and quality. It is the core of inkjet printing. Clogs or burns can severely impact the machine’s operation. Most manufacturers use Epson printheads, with the I3200-A1 being a higher-performance option for demanding applications, offering better longevity.
– Mainboard: The mainboard coordinates all printer components, including the printhead, ink delivery system, and others, to produce high-quality images on the printing medium. Renowned brands include Hansheng boards.
– White Ink Circulation: DTF printers require high white ink fluidity due to its unique composition. Most machines come with a white ink circulation system, including components like circulation pumps and filters.
3. DTF Printer Consumables—DTF Inks
DTF ink is a water-based pigment ink with properties like lightfastness, moisture resistance, and oxidation (including ozone) resistance. This explains why prints using this ink can last long on garments. High-quality inks offer strong color saturation, a wide gamut, high color accuracy, and long-lasting prints.
4. DTF Consumables – DTF Hot Melt Powder
Currently, there are various types of hot melt powders on the market to meet different production needs, such as PA hot melt powder, EVA hot melt powder, and TPU hot melt powder. We recommend using high-purity TPU hot melt powder with DTF printers to achieve flawless heat transfer results. 100% TPU powder offers superior performance due to its clean composition—free from impurities—providing:
– Better stretch resistance
– Clean powder shaking (no residue buildup)
– No powder sticking, ensuring crisp transfer images
– Sharp small text and fine lines without ghosting
– Scratch-resistant and anti-yellowing properties
5. DTF Consumables – PET Film
DTF printing involves printing designs onto PET film or transfer paper, which is then heat-pressed onto garments. PET printing films are categorized into: single-sided coated film and double-sided coated film. They are also classified by peeling temperature: “Cold peel film”, “Warm peel film”, “Hot peel film”.
High-quality DTF transfer materials should have:
– Even coating for consistent ink absorption
– Precise alignment (no slipping during printing)
– Clean powder shaking for smooth transfers
– Excellent release effect (easy peeling)
– Uniform adhesive curing for high wash durability
– Soft hand feel with strong elasticity (no cracking)
Transfer film/paper heat press settings:
– Temperature: 130–160°C (266–320°F)
– Time: 8–15 seconds
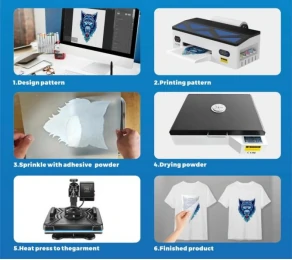